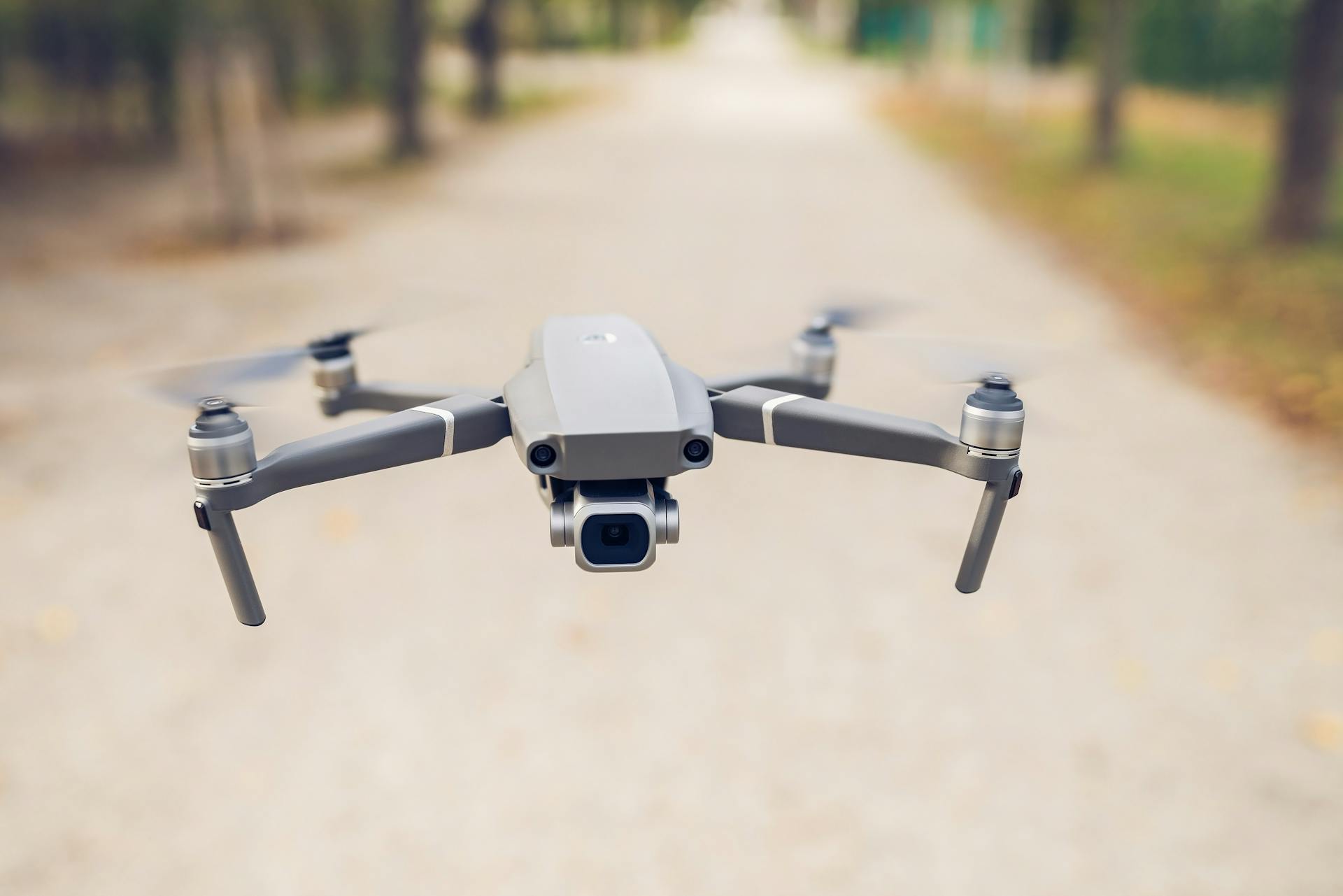
RPAS technology has come a long way in recent years, with advancements in design and functionality making it more accessible and efficient.
The term RPAS stands for Remotely Piloted Aircraft System, which is a critical distinction from traditional drones.
RPAS systems are designed to operate with a high degree of autonomy, allowing them to fly and navigate without human intervention.
These systems can be used for a variety of applications, including surveillance, inspection, and data collection.
Recommended read: Canada Rpas
RPA Components
RPA Components are the building blocks of a Remotely Piloted Aircraft. The airborne component is the most obvious part, which can be a fixed-wing, rotary-wing (like a quadcopter), or hybrid aircraft.
The Remote Pilot Station is where the magic happens, serving as the control hub where the pilot operates the RPA. This station includes flight control software, monitoring displays, and communication interfaces.
The Command and Control Link is the communication channel that connects the RPA to the RPS, facilitating real-time data transmission and control commands.
A fresh viewpoint: Wing Delivery Drones
The Airframe is the physical structure of the RPA, designed for aerodynamics, durability, and payload capacity. It houses all the essential components.
The Propulsion System includes motors and propellers or, for larger RPAs, jet engines. This system provides the necessary thrust for takeoff, flight, and maneuvers.
The Power Source is typically batteries for electric RPAs or fuel for combustion engine-powered RPAs, providing the energy needed for flight operations.
Here are the main RPA components, categorized for easy reference:
Operational Phases
Operating a Remotely Piloted Aircraft System (RPAS) involves several key phases that ensure a successful mission. Each phase is critical to the success of the operation.
Pre-flight planning is where it all starts. This is where the mission is planned, specifying flight paths, waypoints, altitudes, and specific tasks such as data collection points. These details are uploaded to the autopilot system.
The takeoff and launch phase is the next step, where the RPA can be launched either manually by the remote pilot or autonomously, using programmed procedures to achieve the desired altitude and begin the mission.
Mission execution is where the RPA follows the predetermined flight path, performing tasks such as data collection or surveillance. The remote pilot monitors and can adjust the flight plan in real-time if necessary.
The RPA's sensors and cameras capture images, videos, or other data, which can be transmitted back to the RPS for analysis or storage. This data collection phase is crucial for the success of the mission.
The landing and recovery phase is the final step, where the RPA returns to a designated landing area, guided either autonomously or manually by the remote pilot. Safe landing procedures ensure the RPA is ready for subsequent missions.
Here's a breakdown of the operational phases of an RPAS mission:
Applications and Use Cases
Law enforcement agencies use RPAS for surveillance and reconnaissance, allowing remote pilots to gather crucial information safely. This has proven to be a game-changer in keeping communities secure.
RPAS can be used for a variety of tasks, including gathering data and monitoring situations remotely.
For your interest: Army Rpas
RPA Types and Differences
There are several types of RPA, each with its own strengths and weaknesses.
Robotic Process Automation (RPA) can be broadly classified into three categories: attended automation, unattended automation, and hybrid automation.
Attended automation requires human intervention, where a user initiates and monitors the automation process.
Unattended automation, on the other hand, is fully automated and runs independently without human intervention.
Hybrid automation combines both attended and unattended automation, offering flexibility and scalability.
Another type of RPA is Desktop Automation, which automates tasks on a user's desktop, such as data entry and document processing.
Mobile Automation is also a type of RPA, which automates tasks on mobile devices, such as mobile apps and mobile websites.
Some RPA tools also offer Micro Automation, which automates small, repetitive tasks, such as data entry and document processing.
The choice of RPA type depends on the specific business needs and requirements.
You might like: Dji Phantom 3 Standard User Guide
RPA Industry and Design
The Eurodrone MALE RPAS measures an overall length of 16m, a height of 6m, and a wingspan of 26m.
This remotely piloted aerial vehicle can cruise at a maximum speed of approximately 490km/h and has a maximum operational altitude of 45,000ft.
The maximum take-off weight of the UAV is 11 tonnes, while the maximum payload capacity is up to 2,300kg.
The Eurodrone features all-weather capability, efficient maintenance, and 24/7 day and night mission capability.
The maximum flight time of the system ranges between 18 and 40 hours, depending on the mission profile.
The International Civil Aviation Organization (ICAO) employs the acronym RPAS, which stands for Remotely Piloted Aircraft System.
The term RPAS is the preferred terminology used by international aviation-related agencies like ICAO, Eurocontrol, and EASA.
The acronym UAS stands for Unmanned Aerial System, referring to an unmanned aircraft and all its related elements that operate without a pilot on board.
You might like: Unmanned Aerial Systems
RPA Propulsion
The propulsion system of an RPA is a crucial component that provides the necessary thrust for takeoff, flight, and maneuvers. It includes motors and propellers or, for larger RPAs, jet engines.
The airframe is designed to house all the essential components, including the propulsion system. The propulsion system is the heart of the RPA, providing the power needed for flight.
The power source is typically batteries for electric RPAs or fuel for combustion engine-powered RPAs. The choice of power source depends on the specific design and application of the RPA.
Here are the main components of the propulsion system:
- Motors: Provide the mechanical energy needed for propulsion.
- Propellers: Convert the mechanical energy into thrust.
- Jet engines: Used in larger RPAs for high-speed flight.
The propulsion system is designed to be efficient and reliable, with a focus on minimizing weight and maximizing power output. The choice of propulsion system depends on the specific requirements of the RPA, including its intended use and operating environment.
Navigation and Control Systems
Navigation and Control Systems are crucial for the safe and efficient operation of RPAs. The Autopilot System is a key component, managing the RPA's flight path, altitude, and speed using pre-programmed instructions or real-time inputs from the RPS.
The Autopilot System relies on sensors like GPS, gyroscopes, and accelerometers for precise navigation. This ensures that the RPA stays on course, even in challenging weather conditions.
Consider reading: Dji - Mini 2 Se Drone with Remote Control
Manual Control allows the remote pilot to take direct control of the RPA through the RPS. This is particularly useful in situations where the Autopilot System is unable to navigate safely.
The Command and Control link is used to send commands from the RPS to the RPA. This link is essential for Manual Control, allowing the remote pilot to steer the RPA and make adjustments in real-time.
Communication Systems
Communication Systems are a vital component of RPA design, ensuring seamless interaction between the RPA and the RPS. This includes the Command and Control Link, which transmits telemetry data such as position, speed, and altitude in real-time.
The Command and Control Link is a two-way communication system that allows for continuous control inputs and data transmission. This ensures the RPA can receive instructions and transmit its status in real-time.
A Telemetry System is also crucial, providing real-time data about the RPA's status and environmental conditions. This data is essential for safe and effective operation, allowing operators to make informed decisions.
Here are the key components of the Communication Systems:
- Command and Control Link: Ensures continuous communication between the RPA and the RPS.
- Telemetry System: Provides real-time data about the RPA’s status and environmental conditions.
Contractors Involved
The Eurodrone programme has assembled a team of skilled contractors to help bring this innovative RPA to life. DFS Aviation Services, a German provider of air traffic management services and solutions, was contracted for the preliminary safety assessment of the unmanned system in September 2018.
Avio Aero, a GE Aviation business, was chosen by Airbus to supply the Catalyst engine for the Eurodrone UAS in March 2022. This is a significant development, as a reliable engine is crucial for the RPA's performance and safety.
MT-Propeller, a German manufacturer, designed and manufactured the propellers for the Eurodrone. Their expertise in propeller design and manufacturing is evident in the high-quality components they've provided.
GMV, a Spanish technology company, secured a contract to oversee the design, development, production, and logistical support for the ground flight control computer as part of the Eurodrone Programme in September 2022. This contract highlights the importance of a robust ground control system in RPA operations.
Safran Landing Systems, an aircraft landing gear manufacturer, signed a contract with Airbus D&S to supply the wheels and brakes system for the Eurodrone in April 2023. This collaboration ensures that the RPA's landing gear is reliable and efficient.
Hensoldt and Sener’s joint team will provide the Wide Band LoS Ku data link for the Eurodrone programme, complete with advanced cybersecurity features. This is a critical component of the RPA's communication system, enabling secure and reliable data transmission.
Grupo Oesia, an aerospace technology company, secured a contract from Airbus D&S to develop, manage, and support the cypher for the flight test instrumentation of the Eurodrone in April 2024. Their expertise in cybersecurity and data management will be essential in ensuring the RPA's safe and efficient operation.
Eurodrone Design and Features
The Eurodrone MALE RPAS is a remotely piloted aerial vehicle that measures 16m in length, 6m in height, and has a wingspan of 26m. It has a maximum take-off weight of 11 tonnes and can carry a payload of up to 2,300kg.
This aircraft is designed to operate in non-segregated airspace and can fly for 18 to 40 hours, depending on the mission profile. It boasts mission modularity, ensuring operational superiority in wide area and in-theatre intelligence, surveillance, and reconnaissance missions.
The Eurodrone can cruise at a maximum speed of approximately 490km/h and has a maximum operational altitude of 45,000ft. It features all-weather capability and efficient maintenance, making it suitable for 24/7 day and night mission capability.
The UAV is interoperable with existing and future defence systems, and its Line-of-Sight (LoS) Data Links can connect the RPAS with different ground stations for real-time decision-making. It can also carry a variety of payloads and precision weapons for ground support missions.
Frequently Asked Questions
What does RPAS stand for?
RPAS stands for Remotely Piloted Aircraft System, a type of unmanned aircraft controlled from a distance. Learn more about the technology and applications behind RPAS systems.
What is the difference between UAV and RPAS?
While often used interchangeably, UAV refers specifically to the aircraft itself, whereas RPAS encompasses the entire system including the aircraft, control station, and communication links. Understanding the difference is crucial for accurate classification and regulatory compliance.
Sources
- https://altigator.com/en/drone-uav-uas-rpa-or-rpas/
- https://www.flyeye.io/drone-acronym-rpas/
- https://sites.google.com/educause.edu/educause-cg-webpages/remotely-piloted-aerial-systems-rpas
- https://www.airforce-technology.com/projects/european-male-rpas-europe/
- https://umilesgroup.com/en/rpas-uas-and-uav-what-are-they-and-how-do-they-differ/
Featured Images: pexels.com